Robotic Machine Tending
Product image
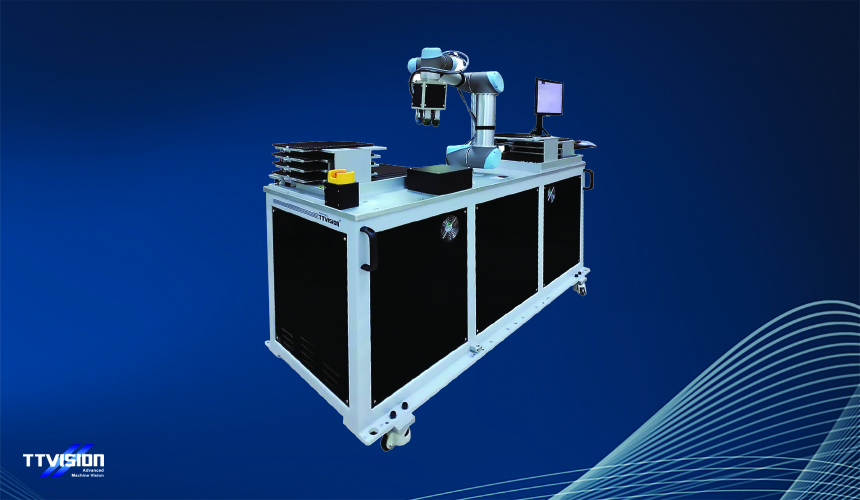
Robotic Machine Tending
Description
The Robotic Machine Tending system, featuring collaborative robots, customized tooling, and advanced vision capabilities, represents a forward-thinking approach to automation. It not only improves efficiency but also ensures the adaptability of your manufacturing processes in a collaborative and lights-out environment.
Features
- Collaborative Robots from Universal Robots (UR):
Harness the power of collaborative robots from Universal Robots (UR). These advanced robots are designed to work alongside human operators, promoting a safe and efficient collaborative working environment. - Tending One or Multiple Machines:
The Robotic Machine Tending system is versatile and capable of tending to one or multiple machines simultaneously. This flexibility optimizes production efficiency and adapts to varying manufacturing needs. - Customized End-Effector and Product Trays:
Tailor the robotic system to your specific manufacturing requirements with customized end-effectors and product trays. This customization ensures seamless integration and handling of diverse products and tasks. - Post-Process Quality Vision Inspection:
Ensure the quality of the manufacturing process with post-process quality vision inspection. The robotic system incorporates advanced vision technology to inspect and verify the quality of the finished products. - Operate Under Lights-Out Environment:
Enhance operational efficiency by enabling the robotic system to operate under lights-out conditions. Lights-out manufacturing ensures continuous production, optimizing resource utilization and minimizing downtime. - Cobot-Equipped Mobile Robot (AGV/AIV):
Integrate collaborative robots (cobots) into a mobile robot system, such as an Automated Guided Vehicle (AGV) or Autonomous Intelligent Vehicle (AIV). This configuration enhances the flexibility and mobility of the robotic system, allowing it to adapt to dynamic manufacturing environments.
Specification
Cobot Payload
3.5 and 10 kg
Repeatability
Up to 30 micron
Product Loading Format
Tray, Cassette, Magazine, etc.
UPH
75
Vision Module Accuracy
+/- 10 Micron
Facility Requirement