Quad Solar Cell Sorter
Product image
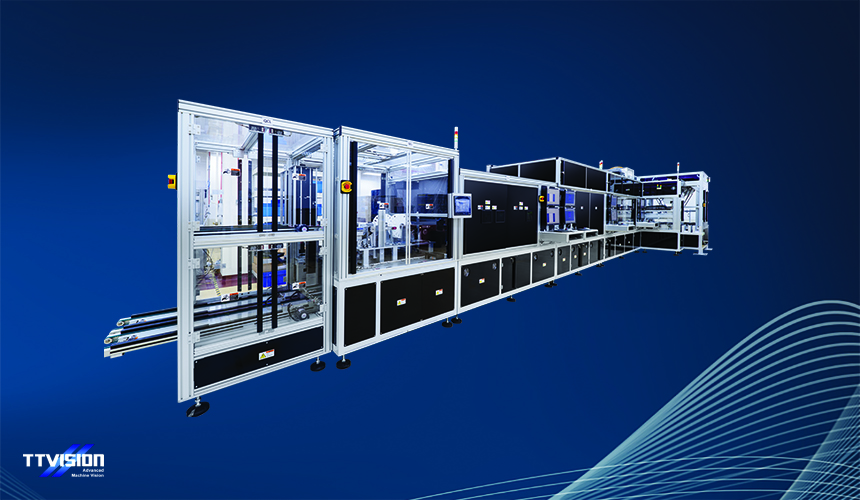
Quad Solar Cell Sorter
Description
This Quad Solar Cell Sorter stands as the pinnacle solution for comprehensive inspection, testing, and sorting of high-quality solar cells. This advanced machine is equipped with a multitude of cutting-edge technologies, including 2D area and line scan, 3D dark field line scan, Photoluminescence (PL) microcrack and solder pads defects inspection, hotspot infrared imaging measurement, and a 3D laser profiler for precise metal line profile measurement. The inclusion of an IV tester, coupled with advanced data analysis capabilities, ensures thorough testing and evaluation of every solar cell.
Features
- Full-Fledged Inspection, Testing, and Sorting Capabilities for IBC Solar Cells:
The Quad Solar Cell Sorter offers comprehensive inspection, testing, and sorting functionalities specifically designed for IBC (Interdigitated Back Contact) solar cells. - Capable of Handling 4 Solar Cells Simultaneously:
This advanced system is capable of handling four solar cells simultaneously, accommodating a broad range of cell sizes from 4 inches to 10 inches. This multi-cell handling capability significantly enhances efficiency in the sorting process. - 2D Colour Area Scan for Front Side Inspection:
Utilize 2D colour area scan technologies for thorough front-side inspection. This dual approach ensures accurate defect detection on the front surface of the solar cells, enhancing overall quality control. - Line Scan for Rear Side Inspection:
Implement line scan technology for rear-side inspection, contributing to a comprehensive analysis of solar cell quality. - 3D Dark Field Line Scan for Rear Side Inspection for Embossed Metallization Defects:
Utilize 3D dark field line scan technology for rear-side inspection, specifically designed to detect embossed metallization defects. This enhances the capability to identify subtle imperfections in the metallization process. - PL for Micro-Crack and Solder Pads Defects Inspection:
Employ photoluminescence (PL) technology for the detection of micro-cracks and solder pads defects. This adds a layer of precision to the inspection process, ensuring the identification of critical defects. - Infrared Imaging for Hot-Spot Measurement:
Utilize infrared imaging for hot-spot measurement, allowing for the identification of temperature differentials within the solar cells. This feature contributes to the overall safety and reliability of the solar modules. - 3D Laser Profiler for Metal Line Profile Measurement:
Implement a 3D laser profiler for accurate metal line profile measurement. This technology ensures precise characterization of metal lines, contributing to the overall performance and efficiency of the solar cells. - 3D Vision Aligner for Cell Positioning and Alignment for Probing:
Benefit from a 3D vision aligner that facilitates precise cell positioning and alignment for probing. This feature ensures accuracy in testing procedures, contributing to the reliability of the sorting process. - I-V Tester and Advanced Data Analysis:
Incorporate an I-V tester for accurate electrical characterization of solar cells. The advanced data analysis capabilities enhance the efficiency of the testing process, providing detailed insights into the performance of each cell. - Laser Scribing and Cleaving for Half-Cut Cell:
Employ laser scribing and cleaving technologies for the production of half-cut cells. This feature enhances the efficiency and precision of cell manufacturing. - Interleaf Paper Placement Before Cell Sorting:
Enhance the handling of solar cells with interleaf paper placement before sorting to fulfill the need for protection and integrity of cells during the sorting process. - Combination of Belt and Walking Beam Conveyor:
Achieve high-speed and high-stability cell transportation with a combination of belt and walking-beam conveyor systems. This dual approach optimizes the transportation process, contributing to overall efficiency. - Throughput up to 8,000 UPH for Dual Track Configuration:
The Quad Solar Cell Sorter boasts an impressive throughput of up to 8,000 units per hour (UPH) for dual-track configuration, ensuring rapid and efficient sorting for high-volume manufacturing.
Machines Integrated
-
Laser Scribing and Cleaving
The Solar Cell Sorter incorporates the QSV module for laser scribing and cleaving, providing a streamlined solution for cleaving half-cut cells post Top Light Inspection (TLI). The module features a conveyor and theta aligner, ensuring a precise cut and subsequent realignment for optimum angles. -
Cell Loader (QCL)
The high-speed Cell Loader module is designed to efficiently unload solar cells from cassettes, minimizing breakage and maximizing production efficiency. The module includes a buffer station for seamless cassette changeovers, a flipper for changing cell orientation, and conveyors for smooth cell transport. The DM Reader ensures essential traceability for quality control. -
Multi Tester (QTT)
The QTT module features a main transportation line with a walking beam and output conveyor. Solar cells are positioned and aligned by the VA aligner, then tested at various stations including the Hot Spot Infrared Tester (HST), Laser Profiler (LP) for metal line profile measurement, Single Flash IV Tester (IVT), and Photoluminescence (PL) for microcrack and solder pads defects inspection. -
Full-Fledged AOI Module (QSV)
Our advanced AOI module is designed for precise surface cosmetic inspection, covering Shallow Angle Sunnyside Area Scan Inspection (SASAI), Rear Vision (RV), Dark Field Inspection (DFI), and Front Vision (FV). This includes 2D color area and line scan for front side inspection, line scan for rear side inspection, and 3D dark field line scan for embossed metallization defects on the rear side. -
Link Module (QLM)
The QLM module accurately places interleaf paper on the sunny side of solar cells and separates them into two sorters. A 4-head pick-and-place robot handles incoming cells, with an alarm indicating when interleaf paper needs refilling. The interleaf bin is automatically indexed out for operator refilling. -
First & Second Sorter (QFS & QSS)
The delta robot swiftly picks up cells and places them in the correct bin as they reach the pickup position. A user-friendly touch screen interface facilitates bin selection for indexing out, ensuring efficient and organized sorting.